From Sparks to Strength: Top Welding Techniques You Should Know
Introduction
From spark to structural bond—that’s the transformative power of welding. In the iLearn Engineering® article “From Sparks to Strength: Top Welding Techniques You Should Know,” readers are guided through essential welding methods—such as SMAW, MIG, TIG, and spot welding—each selected for strength, speed, or precision. Whether it’s the rugged versatility of stick welding or the exacting control of TIG for delicate joints, each technique brings its own strengths and challenges.
But welding is far more than melting metal—it’s about controlling heat, managing material transfer, and mastering joint design to achieve reliable, defect-free bonds. For instance, MIG welding harnesses inert gas to protect the weld pool during high-speed operations, while TIG welding relies on a non-consumable tungsten electrode and optional filler for precision work youtube.com+10machinemfg.com+10weldingproperty.com+10jmweldingsinc.com+1db-sheetmetals.co.uk+1.
This article delves into how each welding method works, where each is best applied, and how engineers andfabricators can select the right technique to align with their production goals—whether you’re constructing a bridge, fabricating automotive parts, or engineering aerospace components.
Every industrial sector that requires the tight connecting of two materials uses bonding as an essential technique. It consists of several different processing techniques that can be categorised under the headings of chemistry, physics, and materials science.
Welding entails applying a proper amount of heat and/or pressure to the contacting surfaces of two or more workpieces so as to create a strong joint. Many welding procedures include applying heat alone, no pressure is used, while others involve using heat along with pressure. Still other welding processes involve applying pressure only, no external heat is used.
A filler substance is sometimes used in welding procedures to speed up coalescence. A weldment is the collective term for the parts that are bonded together by welding.
Although combining polymers by welding is also practised, the use for joining metal is more common. Here, metals will be the main topic of our discussion on welding.
The part surfaces that must be connected and are in touch or close proximity are known as the faying surfaces.Although welding is often done on pieces made of the same metal, there are several welding techniques that can be used to unite metals that are not compatible.
Advantages of welding
1. A permanent joint is provided by welding. The welded components unite to form one whole.
2. If the right welding procedures are followed and a filler metal with stronger characteristics than the parent materials is employed, the welded joint may be stronger than the parent materials.
3. In terms of material utilisation and fabrication costs, joining components through welding is typically the most cost-effective option. Alternative mechanical assembly techniques include more intricate shape modifications (such as drilling holes) and the inclusion of fasteners (such as rivets or bolts). Typically, the final mechanical assembly weighs more than a similar weldment.
4 Welding is not just done in a manufacturing setting. ”In the field” is where it can be done.
Disadvantages of welding
1. The majority of welding tasks are done manually and are labour-intensive. Since many welding procedures are regarded as “skilled trades,” it may be difficult to find someone to carry them out.
2. The majority of welding procedures are inherently risky due to the use of high energy.
3. Welding prevents convenient disassembly since it creates a permanent bond between the parts. Welding should not be utilised as the assembly method if the product needs to be occasionally disassembled (for example, for repair or maintenance).
4. There are some hard-to-find quality flaws that the welded junction may experience. Defects may weaken the joint’s strength.
Different welding procedures
We can categorise the welding procedures into two main categories: fusion welding and solid-state welding, respectively.
Fusion Welding
Heat is used in fusion welding procedures to melt the base metals. In order to speed up the process and give the welded joint bulk and strength, filler metal is frequently added to the molten pool during fusion welding operations. An autogenous weld is a fusion-welding operation in which no filler metal is supplied.
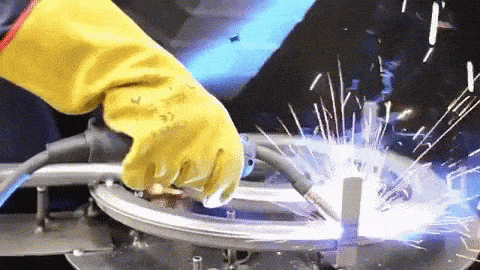
.
Arc welding (AW).The term “arc welding” describes a collection of welding techniques in which the metals are heated using an electric arc. Most arc welding procedures use a filler metal, and some also apply pressure during the welding process.
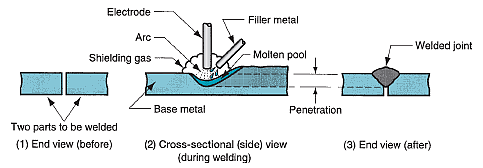
Resistance welding (RW): Resistance welding generates heat by creating an electrical resistance to the flow of a current between the faying surfaces of two components that are compressed together.
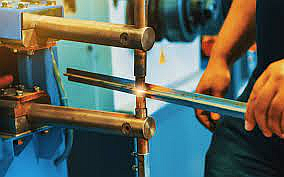
Oxyfuel gas welding: The base metal and filler metal, if any, are melted during these joining operations using a hot flame created by an oxyfuel gas, such as an oxygen-acetylene mixture.
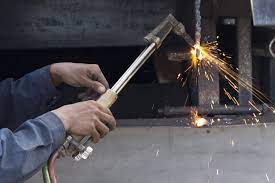
Additional fusion-welding techniques. Electron beam welding and laser beam welding are further welding techniques that result in the fusion of the metals that are connected.
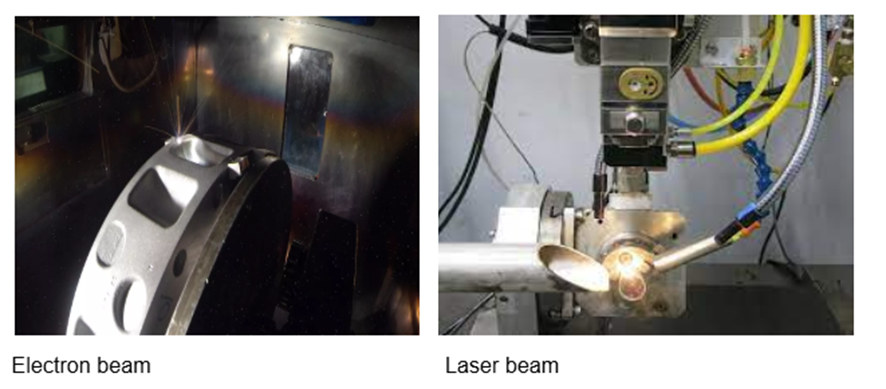
Solid-State Welding
Solid-state welding is the term for joining procedures in which pressure application alone or in conjunction with heat application causes coalescence. Even though heat is applied, the temperature during the welding process is below the melting point of the metals. There is no filler metal used.
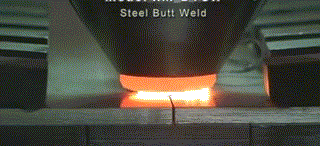
Typical welding procedures in this category include:
Diffusion welding (DFW). The pieces merge by solid-state diffusion when two surfaces are pressed together under pressure at a high temperature.
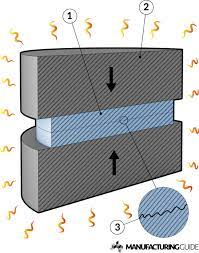
Friction welding, or FRW. Heat from contact between two surfaces causes coalescence.
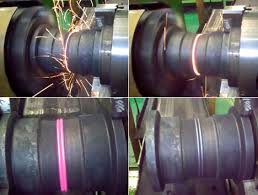
Ultrasonic welding. Ultrasonic oscillations are used in a direction parallel to the contacting surfaces while a moderate amount of pressure is placed between the two components. The removal of surface coatings and attainment of atomic bonding of the surfaces are accomplished by shear stresses produced by the interaction of normal and vibratory forces
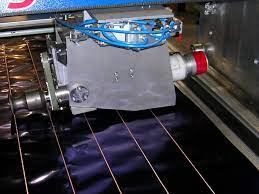
Interested in our engineering courses?
We have over 70 courses across all major engineering disciplines, including, mechanical, electrical and electronic, civil, aerospace, industrial, computer and general engineering. Visit our course catalogue for a complete list of fully accredited engineering programmes.
A small selection of short courses …
Level 6 Courses
International Graduate Diploma in Mechanical Engineering
Level 5 Courses
Higher International Diploma in Industrial Engineering
Higher International Diploma in Mechanical Engineering
Level 4 Courses
Higher International Certificate in Industrial Engineering
Higher International Certificate in Mechanical Engineering
Alternatively, you can view all our online engineering courses here.
Recent Posts
Enhancing Materials: A Look into Surface Treatment Processes
Enhancing Materials: A Look into Surface Treatment Processes Introduction In manufacturing, selecting a material with the right bulk properties is only half the story. The performance of a component often hinges on what happens at its surface. The iLearn Engineering® article explores how various surface treatment processes—from coatings and plating, to shot peening, anodizing, and […]
How Material Removal Rate Affects Surface Quality and Production Speed
How Material Removal Rate Affects Surface Quality and Production Speed Introduction When machining components, one of the most critical—and often overlooked—factors is the material removal rate (MRR). It’s a common assumption that increasing MRR boosts productivity. However, as this iLearn Engineering article explains, this simple equation comes with important trade‑offs. Pushing MRR too high can […]
How Manufacturing Affects the Mechanical Properties of Materials
How Manufacturing Affects the Mechanical Properties of Materials Introduction Manufacturing doesn’t just shape a material—it fundamentally alters how it behaves. Engineers often select materials based on desired properties like strength, ductility, hardness, or fatigue resistance. But those properties are not fixed. They evolve throughout the manufacturing process. This article explores how processes such as casting, […]