How Manufacturing Affects the Mechanical Properties of Materials
Introduction
Manufacturing doesn’t just shape a material—it fundamentally alters how it behaves. Engineers often select materials based on desired properties like strength, ductility, hardness, or fatigue resistance. But those properties are not fixed. They evolve throughout the manufacturing process.
This article explores how processes such as casting, rolling, forging, welding, machining, and heat treatment influence material characteristics by changing the microstructure. For example:
- Forging compresses and aligns the grain structure, improving toughness.
- Heat treatment adjusts phase composition, tuning the balance between hardness and ductility.
- High-speed machining or welding can introduce residual stresses or initiate microcracks.
These changes are not always desirable—but they are predictable. With the right understanding, engineers can use manufacturing not just to shape a part, but to enhance or control its mechanical performance.
Why It Matters
The mechanical properties of a material—such as elastic modulus, yield strength, ductility, and hardness—describe how it responds to external forces. These properties are influenced by temperature, deformation history, and processing conditions.
In design, the goal is often for a component to resist deformation and retain its shape under load. But in manufacturing, the goal is the opposite: to intentionally deform the material—often beyond its yield strength—to give it a desired form. This fundamental contradiction between design and manufacturing creates an important engineering challenge.
For instance, in producing cold-formed steel, a hot-rolled sheet is passed through rollers and bent at room temperature to create the final shape. These forming operations cause plastic deformation, leading to strain hardening. As a result, the material’s strength increases—but so does its brittleness, altering its suitability for different applications
How manufacturing process affect mechanical properties of component material
There are resulting modifications in the properties of materials due to the imposed forces during the manufacturing process (such as the compressive stresses produced during machining).
Chemical composition and material’s internal structure, such as grain size or crystal structure, are what determine a material’s mechanical qualities. Due to the reorganisation of the internal structure, processing may have a significant impact on mechanical properties. Some physical characteristics, like density and electrical conductivity, may be affected by metalworking procedures or heat treatment, but those changes are often negligible.
Additional modifications to a material’s properties can be made through mechanical processes, hot or cold treatments, and radiation exposure. Usually, a change in the material’s microscopic structure causes the property modification. This category includes both heat-treating, which involves temperatures over room temperature, and cold-treating, which involves temperatures below room temperature.
Effect of primary manufacturing processes
The following are the properties of metals which are altered during the casting process:
Fluidity: It evaluates how smoothly the liquid will flow into a mould cavity. The best fluidity is needed in casting cavities with complex shapes. The same holds true for the casting process, which makes use of moulds with quick cooling rates, such as the permanent metal mould technique. When the metal is cast using plaster or investment casting procedures (cooling at a slow rate), poor fluidity is less of an issue. In addition to being a material characteristic, fluidity is also influenced by factors such as casting temperature, mould type, mould temperature, etc.
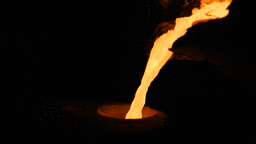
Deficiency in hot cracking: The hot metal has a very low strength when it is solidifying, but it must contract as it cools. There will be strain mismatches in the cooling component as a result of temperature variations. The magnitude of internal stresses that arise during cooling is governed by the elastic modulus. The ductility determines whether these strain mismatches will result in a failure. The metal may not be able to withstand stresses if they are caused by something that prevents the metal from contracting freely, and cracks, also known as hot tears, will appear. In permanent metal moulds, hot tearing is probably a bigger issue than in sand moulds, which are susceptible to collapsing as the casting decreases.
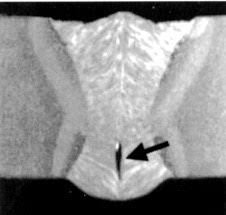
Shrinkage: There is expansion and contraction of most metals during heating and cooling, respectively. The volume of the substance will shrink as it solidifies. Lack of action will cause casting flaws like “lunker” and porosity as a result of this shrinking. So, one of the fundamental things to take into account while sizing the patterns is shrinkage allowance. For each material, the degree of shrinkage is distinctive.
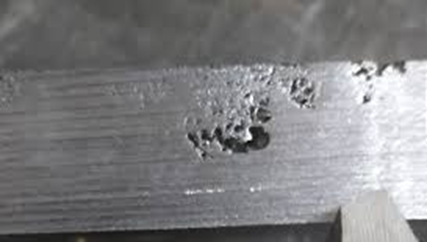
Forming
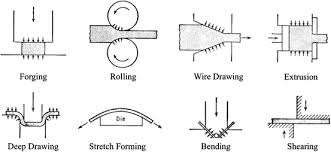
The mechanical properties of the material can be improved and controlled with the use of forming operations. Forging or hot rolling, for instance, can remove blow holes and porosity from a cast ingot, increasing toughness and ductility. With the aid of thermomechanical techniques, there are a lot of opportunities to enhance the qualities.
By utilising the right thermo-mechanical parameters, the grain structure can be improved as well as the physical qualities (such as strength, ductility, and toughness). For instance, strain hardening enhances a metal’s yield strength when cold work is applied to it. The grain flow can also be orientated in the direction of the main stresses present during real use with suitable design.
For instance, forging process improves the following metal properties:
1. There is high ductility and excellent resistance to impact and fatigue stresses in forged parts.
2. Forging improves the metal’s atomic structure.
3. The unidirectional grain flow previously produced by rolling is distorted during forging, which also boosts toughness and strength by determining the direction of the grains.
4. Due to the intense working, defects are rarely discovered, making them highly reliable.
5. Welding the forged components is simple.
However, forging process could also cause detrimental effects on metals, such as:
1. rapid oxidation of the metal surface during forging at a high temperature causes scaling, which erodes the dies.
2. It is challenging to maintain the tight tolerances used in forging processes.
3. if metals are treated below a certain temperature limit, they crack or deform.
More detail on forming can be found here
Joining
The mechanical characteristics of the metals are significantly influenced by welding parameters. Increases in welding current and arc voltage result in decreased yield strength, tensile strength, and impact toughness while increasing hardness. Additionally, the hardness characteristic of the welded samples increases with an increase in welding speed from 40 to 66.67 mm/min.
In summary, joining process such as welding alters the metal’s properties, in that:
1. The workpieces are subjected to residual stresses and distortion.
2. The welded joint requires heat treatment and stress relief.
3. Welding emits dangerous light radiation, gases, and splatter.
4. Fixtures and jigs may also be required to hold and position the welding components.
5. Prior to welding, the welding works must have their edges prepared.
6. Good welding can only be produced by skilled welders.
7. Metallurgical changes are caused by heat during welding because the welded joint’s structure is different from the parent metal’s.
Effect of secondary manufacturing processes
Both turning and milling are two key secondary manufacturing processes that can alter the mechanical properties of materials.
Turning: When turning, the force needed to break the chips apart as the tool moves forward causes severe plastic deformation at the surface and beneath layers. Cold working brought on by this deformation affects the metal’s ductility, hardness, and strength.
As the feed rate rises, the residual stress brought on by the turning process tends to become more compressive. On the other hand, the compressive residual stresses are reduced when the insert’s nose radius is increased. It follows that the feed rate and nose radius are the two most important factors that affect residual stress when turning.
Milling: It has long been understood that free surfaces are where most fatigue cracks start to form. This is because superficial layers are subject to the most stress and environmental influences. The factors affecting the surface layers that cause crack initiation include stress concentration, oxidation, and burning off of alloy components (at high operational temperatures). In most situations, the surface integrity created by machining is what causes crack initiation and propagation.
More information on secondary manufacturing can be found here
Effect of advanced manufacturing processes
Additive Manufacture: powder metallurgy process
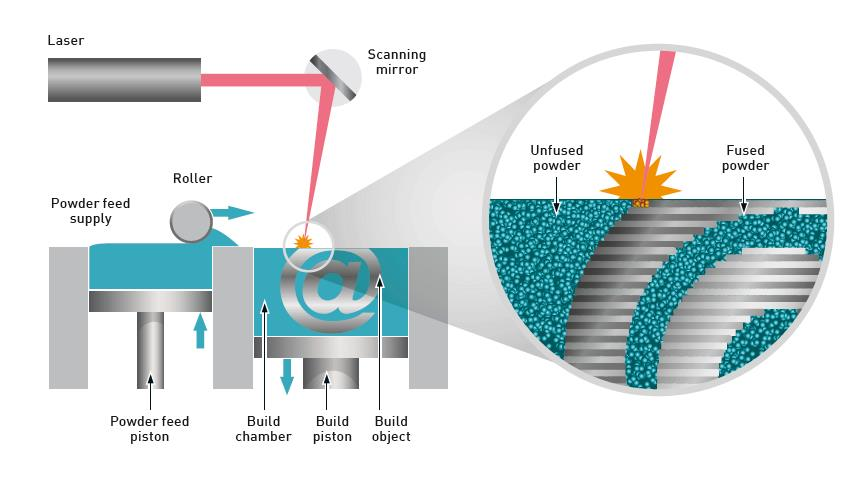
The following properties of metals are modified via the powder metallurgy process:
1. Purity, particle size, density, porosity, and other qualities can all be effectively controlled in the parts made using this technique.
2. This method results in highly pure and long-lasting components.
3. It makes it possible to produce pieces out of such alloys, which have weak casting abilities.
4. Since precise ratios of the constituent metal powders can be employed, composition consistency can be ensured.
5. The preparation and processing of powdered iron and nonferrous parts made in this manner demonstrate excellent qualities that can only be generated in this manner.
6. It is possible to control the size of the grains, create a somewhat homogeneous structure, and get rid of structural flaws like cavities and blowholes.
Other effects of advanced manufacturing process on materials includes:
Defects in the fusion and porosity: One of the key elements contributing to the start of fractures in the manufactured parts for addictive substances is porosity, which is a material discontinuity. Metallurgical pores, also known as spherical pores, are uniformly shaped and small (below 100 µm).
They result from the pores in the gas-atomized powder particles, or when the scan speed is slow, they may be caused by the trapped gas during solidification. Keyhole pores are atypically shaped and have a diameter of more than 100 m. Fast scan speeds tend to produce more of these pores because the substrate solidifies more quickly and the molten pool doesn’t have enough time to completely fill the substrate.
Microcracks caused by residual strains and heat: Because addictive manufactured metal components are built up layer by layer using a lot of heat, it is impossible to avoid having large temperature gradients. Localised heating and cooling induce residual stresses, which are extremely harmful for AM parts because they lower the elastic limit locally and hasten collapse. The key process parameter that needs to be taken into account is the cooling speed, and it was shown that the scan speed had little to no impact on residual stresses. Larger residual stresses are caused by faster cooling rates.
More information on advanced manufacturing techniques can be found here.
Interested in our engineering courses?
We have over 70 courses across all major engineering disciplines, including, mechanical, electrical and electronic, civil, aerospace, industrial, computer and general engineering. Visit our course catalogue for a complete list of fully accredited engineering programmes.
A small selection of short courses …
Level 6 Courses
International Graduate Diploma in Mechanical Engineering
Level 5 Courses
Higher International Diploma in Industrial Engineering
Higher International Diploma in Mechanical Engineering
Level 4 Courses
Higher International Certificate in Industrial Engineering
Higher International Certificate in Mechanical Engineering
Alternatively, you can view all our online engineering courses here.
Recent Posts
From Sparks to Strength: Top Welding Techniques You Should Know
From Sparks to Strength: Top Welding Techniques You Should Know Introduction From spark to structural bond—that’s the transformative power of welding. In the iLearn Engineering® article “From Sparks to Strength: Top Welding Techniques You Should Know,” readers are guided through essential welding methods—such as SMAW, MIG, TIG, and spot welding—each selected for strength, speed, or […]
Enhancing Materials: A Look into Surface Treatment Processes
Enhancing Materials: A Look into Surface Treatment Processes Introduction In manufacturing, selecting a material with the right bulk properties is only half the story. The performance of a component often hinges on what happens at its surface. The iLearn Engineering® article explores how various surface treatment processes—from coatings and plating, to shot peening, anodizing, and […]
How Material Removal Rate Affects Surface Quality and Production Speed
How Material Removal Rate Affects Surface Quality and Production Speed Introduction When machining components, one of the most critical—and often overlooked—factors is the material removal rate (MRR). It’s a common assumption that increasing MRR boosts productivity. However, as this iLearn Engineering article explains, this simple equation comes with important trade‑offs. Pushing MRR too high can […]