Inside the World of Metal Machining: Behaviours and Challenges
Introduction
In the world of modern manufacturing, metal machining remains a cornerstone process, yet it’s far from simple. As detailed in the iLearn Engineering article, machining metals—whether through turning, milling, drilling, or grinding—involves navigating a complex interplay of material properties, tool dynamics, and process parameters.
Metals differ widely in machinability, a concept influenced by factors like hardness, ductility, thermal conductivity, and grain structure. Materials like aluminum are easy to work with, while nickel alloys and titanium challenge even the most advanced machining centers due to their resistance to cutting and tendency to work harden.
Crucially, heat and forces generated during machining can cause tool wear, surface damage, and vibrations (chatter)—each impacting precision, surface finish, and production efficiency. Beyond these technical hurdles, engineers must also optimize for material removal rates, balancing productivity with thermal and mechanical constraints.
This article unpacks how mastering metal machining means understanding more than just geometry—it means orchestrating a symphony of metallurgical science, cutting-edge tooling, and precise process control. It’s this deep insight that empowers engineers to achieve tight tolerances, extend tool life, and hit high-volume production targets with confidence.
Metal machining plays a critical role in modern manufacturing, shaping the raw materials that form the backbone of countless industries, from aerospace and automotive to construction and medical devices. However, machining metals is far from straightforward. Each metal, whether it’s a ductile aluminium alloy or a toughened steel, exhibits unique behaviours under cutting conditions that influence tool selection, machining parameters, surface finish, and overall efficiency.
Alloy Steels and Steels:
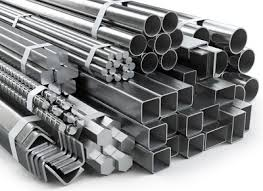
The presence of sulphur in iron and steel (up to 0.35%) aids in chip breaking and increases machinability. Lead helps easy machining by acting as a lubricant at the tool tip. It is also preferable to have nitrogen present. Another ingredient that contributes to improved machinability is phosphorus. The most significant engineering material is steel. By adding alloying elements, they lose a lot of their machinability. Al and Si are always hazardous when present in steels because they react with oxygen to generate aluminium oxide and silicates.
These substances are abrasive and hard, which makes them less machinable and increases tool wear.
Depending on their composition, carbon and manganese have different effects on the machinability of steels. Although machinability declines as carbon content rises, simple low-carbon steels (less than 0.15% C) can nevertheless yield subpar surface finishes by creating a built-up edge (BUE). Tool and die steels are challenging to machine and frequently need to be annealed first. Cold working has typically increased the machinability of most steels and decreased the likelihood for BUE development.
Ni, Cr, Mo, and V are additional alloying elements that enhance the characteristics of steels while reducing their machinability.
Stainless steels:
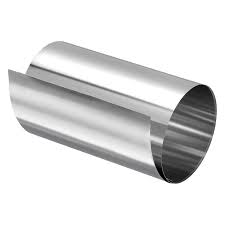
Higher cutting temperatures are a result of stainless steel’s greater strength and less thermal conductivity. Austenitic stainless steels (AISI 300 series) are more difficult to manufacture due to their high rate of strain hardening. However, ferritic stainless steels (also known as AISI 300 series) have good machinability. Chatter could be an issue, necessitating the use of robust machine tools with high stiffness and damping capacity.
Due to its abrasiveness, propensity to generate BUE, and need for tool material with a high hot hardness and resistance to crater wear, martensitic steels (AISI 400 series) are abrasive.
Due to the strength and abrasiveness of precipitation-hardening stainless steels, abrasion-resistant tool materials are necessary. Cutting fluids containing extreme pressure (EP) compounds must be utilised when milling stainless steels. Sulphur, phosphorus, selenium, tellurium, lead, and bismuth are examples of alloying elements that can be used to impart free-machining qualities if necessary. These grades are very vulnerable to pitting corrosion attack and have much reduced corrosion resistance.
The following are some general guidelines for machining stainless steels:
• The machine tools must be reliable, powerful, and vibration-free.
• The cutting edge must always be kept sharp. Glazing and work hardening of the machined surface are caused by dull tools.
• Freehand sharpening should be avoided and should only be done with the proper fittings.
• Cuts should be deep enough to prevent the tool from riding the work surface, which encourages the hardening of the work.
• To improve heat dissipation, tools should be as big as feasible.
• It is recommended to utilise tools with an appropriate clearance angle and chip breakers.
• Proper lubricants and coolants are crucial. They must be utilised in adequate amounts and in a manner that floods the tool and workpiece.
Cast Irons:
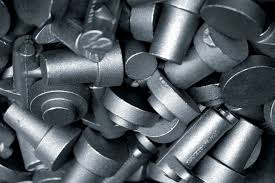
White cast irons are extremely difficult to manufacture because of the presence of primary cementite.
Tools need to be very robust because chill zones in castings limit machinability and lead to chipping or fracture of tools. The graphite lamella breaks up the chips, making grey cast irons essentially free to machine. But because graphite particles escape during machining, the surface is rough. The finish can be improved through refinement without affecting the free-machining capabilities. Because fine chips clog filters, grey cast irons are frequently dried up. Cast irons that are nodular and malleable are ductile and stronger, but they can also be machined and, surprisingly, have a longer tool life.
Nonferrous Metals and Alloys:
Below is a brief overview of the machining characteristics of some significant nonferrous metals and alloys:

Magnesium and its alloys: Due to its low ductility, magnesium is a highly machinable material that offers good surface polish and extended tool life. Oil-based cutting fluids are always used when cutting materials with chip thicknesses below 25 m because very thin chips spontaneously ignite (pyrophoric). BUEs are formed from Mg-Al alloys.
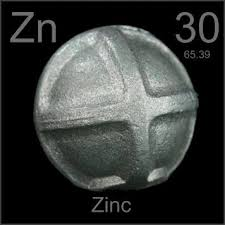
Zn alloys are extremely machinable due to their low strength and low ductility.
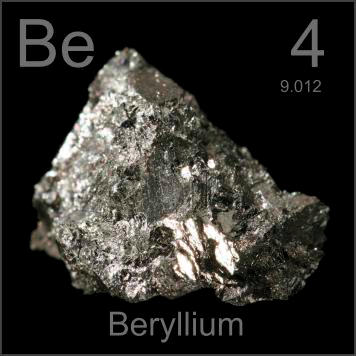
Beryllium (Be) is very easy to machine; dry machining is used. Because hazardous fine particles are produced, machining must be done in a controlled setting.
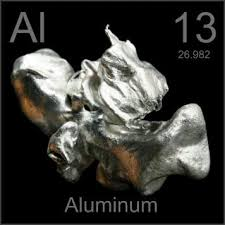
Al and its alloys are relatively simple to manufacture, however the softer grades have a propensity to create BUE. High rake, clearance angles, and cutting speeds are strongly advised.
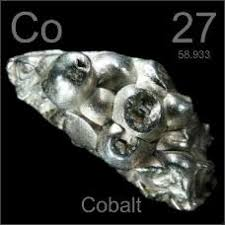
Co-base alloys: These materials are very work-hardening, abrasive, and require low feeds and speeds as well as sharp, abrasion-resistant tools.
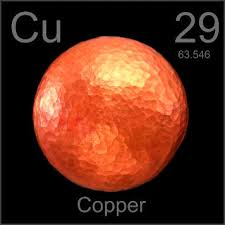
Cu and Cu-base alloys: Cast Cu alloys are simple to manufacture, while pure Cu is challenging due to BUE production. Like pure Al, pure Cu works best when it has been cold-worked.
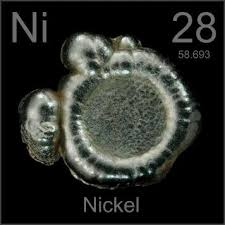
Ni-base alloys are strong at high temperatures, abrasive, and work-hardening. They are machinable in a manner akin to stainless steels. Their machining ought to be carried out in the overaged or annealed condition. Because it forms a low melting eutectic with nickel, sulphur must be avoided in cutting fluids.
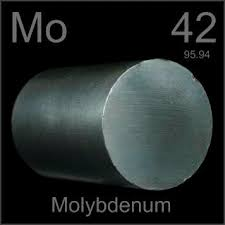
Molybdenum: Because it is ductile and work-hardening, it can provide a poor surface finish, necessitating the employment of sharp tools.
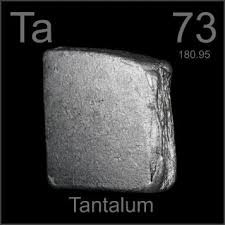
Tantalum provides poor surface finishes and has high tool wear because it is soft, ductile, and very work hardening.
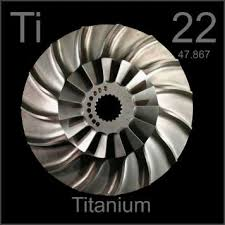
Ti and Ti alloys are difficult to manufacture because they have limited thermal conductivity (the lowest of all metals), which results in high temperature rise and BUE. High speed steel (HSS) tools are used with a heavily formulated oil or emulsion at low speeds. Cemented carbides or cermets are preferable at faster speeds (30–60 m/min). Because frictional heat is decreased and more heat is removed in the chip, heavier feeds are preferable.
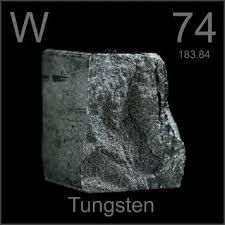
Tungsten has a low machinability because it is brittle, strong, and extremely abrasive. If machining is done at a high temperature, it becomes steadily more machinable.
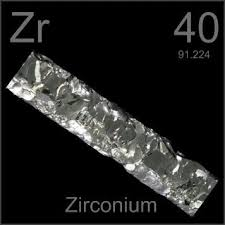
Zirconium is machinable but must be cut with a coolant-type cutting fluid to reduce the risk of fire and explosion
Interested in our engineering courses?
We have over 70 courses across all major engineering disciplines, including, mechanical, electrical and electronic, civil, aerospace, industrial, computer and general engineering. Visit our course catalogue for a complete list of fully accredited engineering programmes.
A small selection of short courses …
Level 6 Courses
International Graduate Diploma in Mechanical Engineering
Level 5 Courses
Higher International Diploma in Industrial Engineering
Higher International Diploma in Mechanical Engineering
Level 4 Courses
Higher International Certificate in Industrial Engineering
Higher International Certificate in Mechanical Engineering
Alternatively, you can view all our online engineering courses here.
Recent Posts
From Sparks to Strength: Top Welding Techniques You Should Know
From Sparks to Strength: Top Welding Techniques You Should Know Introduction From spark to structural bond—that’s the transformative power of welding. In the iLearn Engineering® article “From Sparks to Strength: Top Welding Techniques You Should Know,” readers are guided through essential welding methods—such as SMAW, MIG, TIG, and spot welding—each selected for strength, speed, or […]
Enhancing Materials: A Look into Surface Treatment Processes
Enhancing Materials: A Look into Surface Treatment Processes Introduction In manufacturing, selecting a material with the right bulk properties is only half the story. The performance of a component often hinges on what happens at its surface. The iLearn Engineering® article explores how various surface treatment processes—from coatings and plating, to shot peening, anodizing, and […]
How Material Removal Rate Affects Surface Quality and Production Speed
How Material Removal Rate Affects Surface Quality and Production Speed Introduction When machining components, one of the most critical—and often overlooked—factors is the material removal rate (MRR). It’s a common assumption that increasing MRR boosts productivity. However, as this iLearn Engineering article explains, this simple equation comes with important trade‑offs. Pushing MRR too high can […]