What is casting and why is it important in Engineering?
The first stage of any manufacturing process is to turn the raw material into a usable shape or billet. We call this first step the primary manufacturing processes and we will introduce the 3 main types, casting, forming, and joining.
Close dimensional tolerance cannot be achieved by these processes. Achievable surface finish and surface integrity of the products are also generally poor, as is the appearance. However, these processes are necessary to give a basic property, shape and size so that it can be further processed in the secondary manufacturing processes.
As well as changing the shape of the raw material, this first stage may also alter the material properties of the material, such as its hardness.
This blog will focus on the process of casting
Fundamentally, casting is a process where molten material is poured into a mold which contains a void of the basic shape of the item you wish to cast. The molten material is then allowed to solidify, and you are left with the cast of the item you wanted to produce.

Metal casting is defined as the process in which molten metal is poured into a mould that contains a hollow cavity of a desired geometrical shape and allowed to cool down to form a solidified part.
The term ‘casting’ is also used to describe the part made by the casting process which dates back 6000 years. Historically it is used to make complex and/or large parts, which would have been difficult or expensive to manufacture using other manufacturing processes.Many engineering systems consist of components which oscillate or vibrate in the presence of appropriate forces. This may be desirable or undesirable, or simply unavoidable. A theoretical understanding of the nature of vibration allows us to analyse and solve a wide range of engineering problems. In fact, many of the systems, including engines, presses, unbalanced rotors, and machines with belt drives, may all experience vibration in operation.
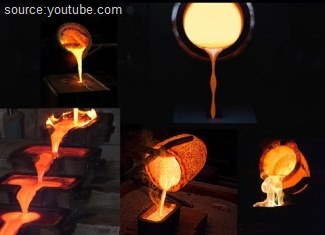
Primarily, casting produces ingots and shapes. An ingot is a casting produced into a simple shape and intended for further processing such as metal extrusion, forging, etc. Shape casting is for near or net shape castings to produce complex geometries which are closer to the final part.
Types of Casting
Casting can be divided into two groups by the basic nature of the mould design. i.e. expendable mould and permanent mould castings. It can be further subdivided into groups depending on their pattern material.
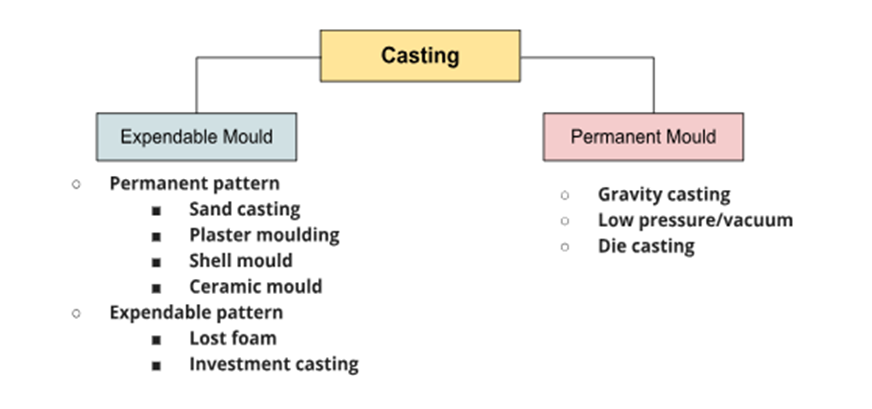
The following factors need to be considered before choosing a suitable metal casting for a given engineering product design.
- Part shape and size
- Required quantity
- Required tolerance
- Material
Expendable mould casting
Expendable mould casting, as the name suggests uses a temporary non-reusable mould to produce the final casting as the mould will be broken to get the casting out. These moulds are typically made of materials such as sand, ceramics & plaster. These are generally bonded using binders called bonding agents to improve its properties. Complex intricate geometries can be cast using expendable mould casting.
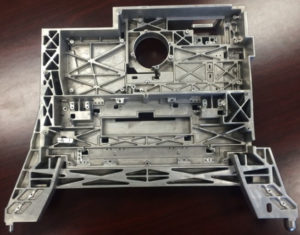
Aluminium alloy a356 copier frame plaster mould aluminium casting
Permanent mould casting
Sometimes called non-expendable mould casting, permanent mould casting uses permanent moulds that are reused after each production cycle. Although permanent mould casting produces repeatable parts due to re-use of the same mould, it cannot produce casts with horizontal voids or overhangs, as the mould cannot be broken to remove the casting.
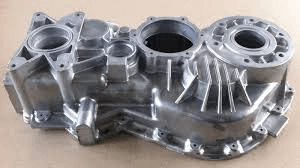
Composite mould casting
As the name suggests this uses both expendable and reusable casting moulds to produce castings. These normally include materials such as sand, wood, graphite and metal.
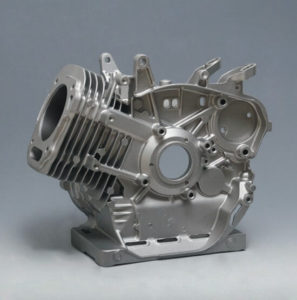
How does metal casting work?
Metal casting steps
- Patternmaking – A replica of the part to be cast is made using a suitable material such as wood, metal plastic or plaster.
- Mould making – Mould making is a multi-step process in which patterns and cores are used to create a mould. The type and how the moulds are made would vary depending on the type of metal casting. For example, sand casting uses sand inside a flask to create moulds and die casting uses hardened tool steel moulds.
- Metal melting & pouring – Liquid is then melted and poured into the mould cavity either by gravity or by high pressure. Then the cast is allowed to solidify before the cast parts are removed from the mould. Again, the cast part removal will vary depending on the type of metal casting.
- Post processing – In this final step, the cast metal object is removed from the mould and then fettled. During the fettling, the object is cleaned of any moulding material, and rough edges are removed.
Elements of the gating system
One of the most common metal casting processes is Sand casting and its mould is made of two halves. Contained inside a box called flask, the upper half is called the cope and the bottom half is called the drag. As shown in the image below the flask is also divided into two halves. The line that separates the two halves is called the parting line.
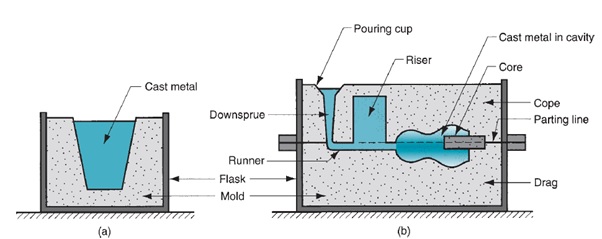
Metal casting gating system (source: Groover (2010))
The gating system is the channel or the path by which the molten metal flows into the cavity. As shown above, the gating system consists of a pouring cup and a down sprue through which the metal enters the runner that leads into the main cavity. The pouring cup minimises the splash and turbulence when the metal flows through the sprue which is tapered to aid the flow. Most of the casting suffers from shrinkage during cooling and to minimise the shrinkage issue, a riser is used. A riser is a simple reservoir in the mould that feeds molten material to the shrinking sections to compensate as it solidifies. There are four different types of risers, viz. top riser, side riser, blind riser and open riser.
Material suitability
Although almost all the metals can be used, the most common ones are iron, steel, aluminium, magnesium and copper-based alloys such as bronze.
Zinc, aluminium, magnesium and brass are widely used in die casting whereas aluminium alloy, brass alloy, cast iron and cast steel are very popular sand-casting materials.
Typical application
Nearly every engineering product we use from washing machines to pillar drills, cars to bicycles are manufactured using metal parts which are most likely to be made using one of the metal casting processes. This age-old manufacturing process has improved its precision and tolerances over time.
Typically, castings are used to make car engine blocks, crankshafts, power tool housings such as pillar drills, plumbing parts, turbine blades, metal statues, some gears and gearbox housings.
Advantages of metal casting
- Metal casting can produce complex shapes
- Features like internal cavities or hollow sections can be easily achieved
- Large components can be produced in one-piece cast
- Materials that are difficult or expensive to manufacture using other manufacturing process can be cast
- Compared to other manufacturing processes, casting is cheaper for medium to large quantities
- Almost all the metals can be cast
- Near net shape often without or very minor post-processing
Because of the above reasons metal casting is one of the important net shape manufacturing technologies. Others include net shape forging, stamping of sheet metal, additive manufacturing and metal injection moulding.
Disadvantages of metal casting
- Relatively coarse surface finish and hence wider tolerance has to be allowed and not suitable for mating interfaces
- Metal casting such as shell moulding has a limit in terms of size and the pattern
- Patterns are time-consuming and expensive to make although additive manufacturing processes such as binder jetting are being used lately to make a mould
- Die casting can be very expensive for smaller to medium quantities due to high die cost
- Part size and material choices depend on the casting process chosen. For instance, only non-ferrous metal can be used for permanent mould castings.
Interested in our engineering courses?
We have over 70 courses across all major engineering disciplines, including, mechanical, electrical and electronic, civil, aerospace, industrial, computer and general engineering. Visit our course catalogue for a complete list of fully accredited engineering programmes.
A small selection of short courses …
Level 6 Courses
International Graduate Diploma in Mechanical Engineering
Level 5 Courses
Higher International Diploma in Industrial Engineering
Higher International Diploma in Mechanical Engineering
Level 4 Courses
Higher International Certificate in Industrial Engineering
Higher International Certificate in Mechanical Engineering
Alternatively, you can view all our online engineering courses here.
Recent Posts
From Sparks to Strength: Top Welding Techniques You Should Know
From Sparks to Strength: Top Welding Techniques You Should Know Introduction From spark to structural bond—that’s the transformative power of welding. In the iLearn Engineering® article “From Sparks to Strength: Top Welding Techniques You Should Know,” readers are guided through essential welding methods—such as SMAW, MIG, TIG, and spot welding—each selected for strength, speed, or […]
Enhancing Materials: A Look into Surface Treatment Processes
Enhancing Materials: A Look into Surface Treatment Processes Introduction In manufacturing, selecting a material with the right bulk properties is only half the story. The performance of a component often hinges on what happens at its surface. The iLearn Engineering® article explores how various surface treatment processes—from coatings and plating, to shot peening, anodizing, and […]
How Material Removal Rate Affects Surface Quality and Production Speed
How Material Removal Rate Affects Surface Quality and Production Speed Introduction When machining components, one of the most critical—and often overlooked—factors is the material removal rate (MRR). It’s a common assumption that increasing MRR boosts productivity. However, as this iLearn Engineering article explains, this simple equation comes with important trade‑offs. Pushing MRR too high can […]