How to describe and analyse damped vibration problems involving a single degree of freedom?
In this blog, we shall review the mathematical analysis of single degree of freedom lumped parameter systems with damping.
For more information about damping click here
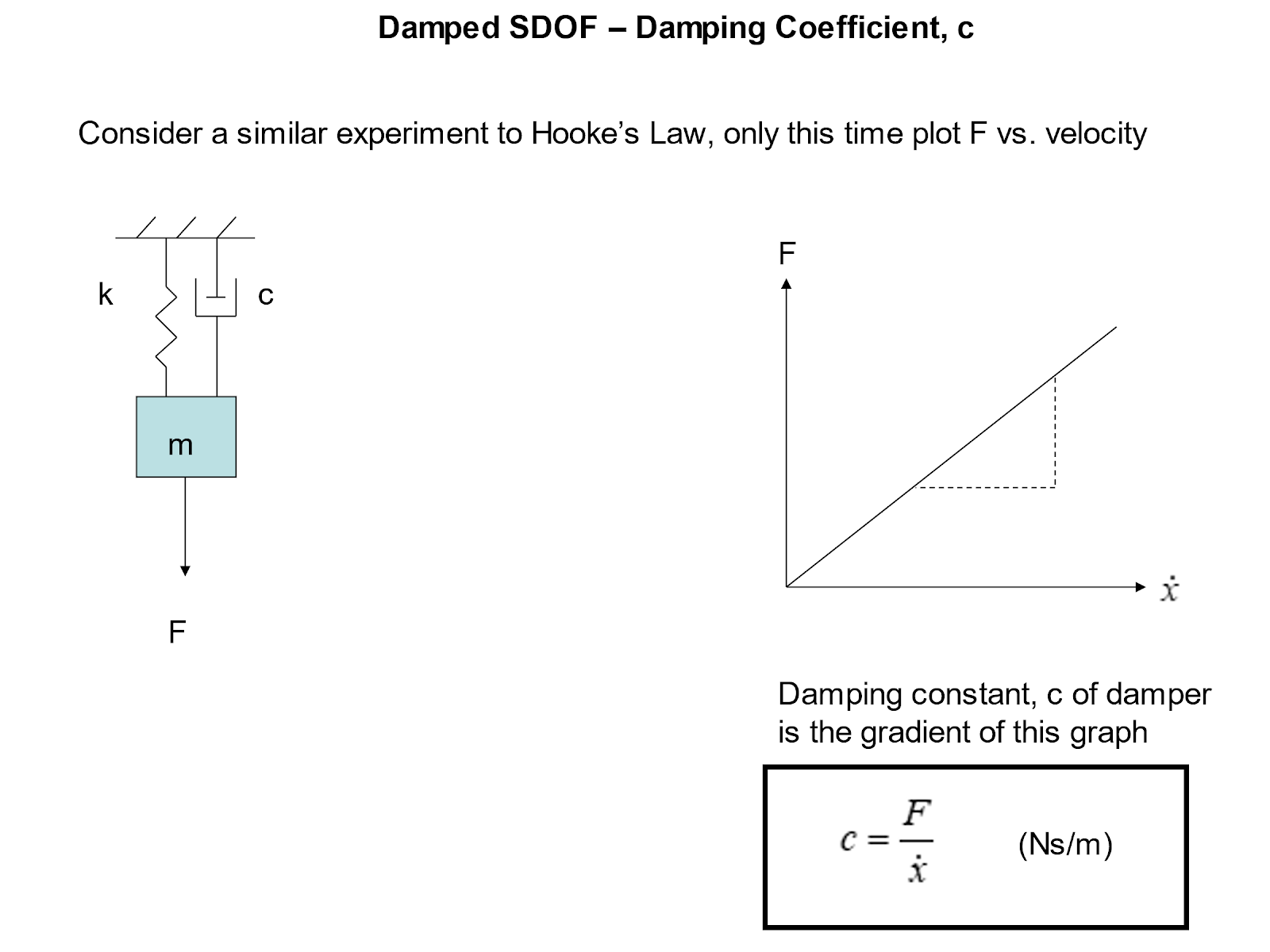
The damping constant, c, is analogous to the spring constant, k, with the difference being that the force is proportional to velocity (whereas that force was proportional to displacement for a spring).
If we consider the damped system in equilibrium as before and analyse the forces acting on the mass in a free body diagram (FBD) as shown below, it is possible to obtain the equation of motion via Newton’s second law as shown.
It can be seen that the equation of motion is similar to that for the undamped system, with the addition of an extra term to account for the damping now present in the model.

If we now normalise with respect to mass (this means to divide through the equation by the mass) we obtain an alternative form of the equation of motion as shown below. This normalised version of the equation of motion can be used to infer the modal parameters of the system, namely the undamped natural frequency, ωn and the damping ratio, ६
These modal parameters are distinct from the physical parameters of the system, and it is possible to describe the equation of motion either in physical parameters or modal parameters with no loss (or duplication) of information.

Let us now consider the response of the system to various amounts of damping. The damping ratio,६, can be either under damped, over damped or critically damped as shown below.
Critical damping is the reference case, because here the damping in the system is such that there is no overshoot in the response, i.e. the system decays to zero without passing the equilibrium position.
Typically, most engineering structures are lightly damped and have a damping ratio value in the single figures as a percentage. Here, there is overshoot followed by several oscillations before the system comes to rest.
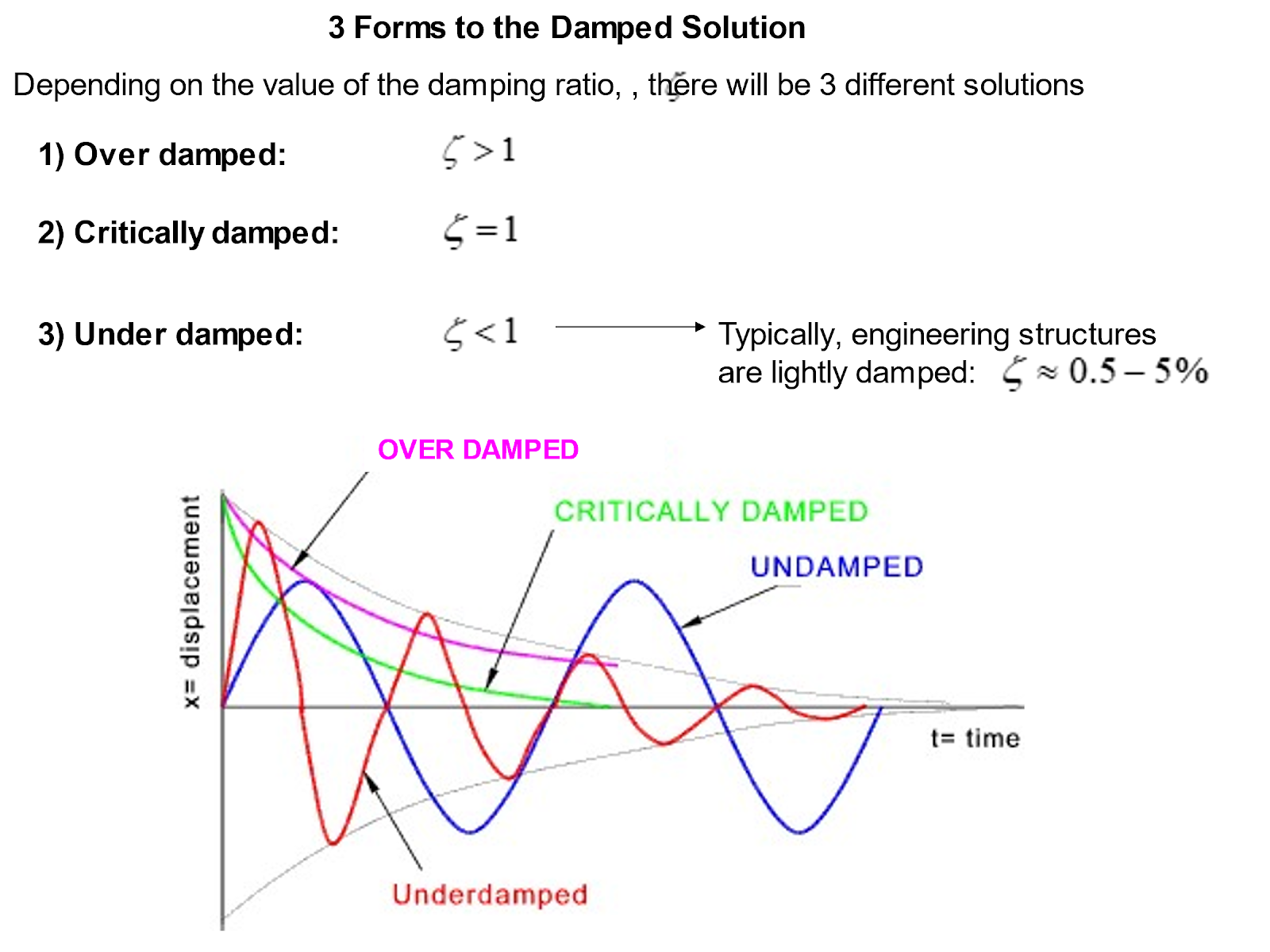

Damped Natural Frequency, ωd and Damped Time Period, Td
The inclusion of damping in a system, has the effect of reducing the resonance frequency slightly which is said to occur at the damped natural frequency, ωd given by:
ωd = ω n √1-६2
Now, as ६ is typically ~ 0.5 – 5%, then it is clear that for light damping:
ωd ≈ ω n
Note, that the time period is also slightly modified and is referred to as the damped time period, Td, :
Td = 1/fd = 2π / ωd
Finally, the time solution for the damped SDOF system can be summarised as follows:
This occurs ६ < 1 and c < cc. If we assume that t = 0 and the displacement, x = A at the moment the mass is released we get a decaying cosinusoidal oscillation as shown. The displacement is described by the following equation.
x = Ae-६ωnt cos( ωdt)

Example 1:
A mass of 4 kg is suspended on a spring of stiffness 3000 N/m. The system is fitted with a damper with a damping ratio of 0.2. The mass is pulled down 50 mm and released. Calculate the following.
a) the damped natural frequency.
b) the displacement after 0.5 seconds
Solution:
a)
ωd = √k/m = √3000/4 = 27.4 rad/s
ωd = ω n √1-६2
ωd = (27.4) √1- (0.2)2 = 26.8 rad/s
b) Displacement:
A=initial displacement = 25 mm = 0.025 m
x = Ae-६ωnt cos( ωdt)
x = 0.025 e -(0.2)(27.4)(0.5) cos (26.8 x 0.5)
x = 0.025 e -(2.74) cos (13.4)
x = 0.025 ( 0.065)(0.67) = 1.08 X 10-3 m
x = 1.08 mm
Example 2:
A product with a mass of 2 kg is mounted on a spring which experiences a 0.5 mm extension when a force of 1.2 N is applied to it. A viscous damper system is also attached to the product which resists the motion with a force proportional to velocity equal to 25 N when the velocity is 5 m/s.
a)Find the undamped natural frequency, the damping ratio and the damped natural frequency.
b)Comment on the values found for the undamped and damped natural frequencies.
c) Find the time period of the system
d) state the equation of motion for the system
Solution
a)
k = F/x = 1.2 / 0.5 x10-3 = 2400 N/m
c = F / = 25 / 5 = 5 Ns/m
Undamped natural frequency:
ωd = √k/m = √2400/2 = 34.6 rad/s
Critical damping constant is:
cc = 2ωn m
cc = 2(34.6)(2) = 138.6 Ns/m
Damping ratio is:
c = 2६ωn m
६= c / 2ωn m = c/cc
६ = 5 /138.6 = 0.036 = 3.6%
Damped natural frequency:
ωd = ω n √1-६2
ωd = (34.6) √1-(0.036)2
ωd = (34.6)(0.999) ≈ 34.6 rad/s
b) The undamped and damped natural frequencies are very similar. The reason is due to the value of √1-६2 which will take the value of √≈1 ≈1 when the value of the damping ratio,६<<1 (is very small).
c) Time period:
T = 1 / f
ωn = 2π f
Therefore:
f = ωn / 2π
f = 34.6 / 2π
f = 5.5 Hz
Hence:
T = 1 / f = 1/ 5.5 = 0.18 s
d) Equation of motion for free vibration in general terms is:
m + c + kx = 0
In our case:
2 + 5 +2400x = 0
Interested in our engineering courses?
We have over 70 courses across all major engineering disciplines, including, mechanical, electrical and electronic, civil, aerospace, industrial, computer and general engineering. Visit our course catalogue for a complete list of fully accredited engineering programmes.
A small selection of short courses …
Diploma in Mechanical Engineering
Diploma in Structural Engineering
Level 6 Courses
International Graduate Diploma in Mechanical Engineering
International Graduate Diploma in Civil Engineering
International Graduate Diploma in Aerospace Engineering
Level 5 Courses
Higher International Diploma in Mechanical Engineering
Higher International Diploma in Civil Engineering
Higher International Diploma in Aerospace Engineering
Level 4 Courses
Higher International Certificate in Mechanical Engineering
Higher International Certificate in Civil Engineering
Higher International Certificate in Aerospace Engineering
Alternatively, you can view all our online engineering courses here.
<
Recent Posts
From Sparks to Strength: Top Welding Techniques You Should Know
From Sparks to Strength: Top Welding Techniques You Should Know Introduction From spark to structural bond—that’s the transformative power of welding. In the iLearn Engineering® article “From Sparks to Strength: Top Welding Techniques You Should Know,” readers are guided through essential welding methods—such as SMAW, MIG, TIG, and spot welding—each selected for strength, speed, or […]
Enhancing Materials: A Look into Surface Treatment Processes
Enhancing Materials: A Look into Surface Treatment Processes Introduction In manufacturing, selecting a material with the right bulk properties is only half the story. The performance of a component often hinges on what happens at its surface. The iLearn Engineering® article explores how various surface treatment processes—from coatings and plating, to shot peening, anodizing, and […]
How Material Removal Rate Affects Surface Quality and Production Speed
How Material Removal Rate Affects Surface Quality and Production Speed Introduction When machining components, one of the most critical—and often overlooked—factors is the material removal rate (MRR). It’s a common assumption that increasing MRR boosts productivity. However, as this iLearn Engineering article explains, this simple equation comes with important trade‑offs. Pushing MRR too high can […]