Enhancing Materials: A Look into Surface Treatment Processes
Introduction
In manufacturing, selecting a material with the right bulk properties is only half the story. The performance of a component often hinges on what happens at its surface. The iLearn Engineering® article explores how various surface treatment processes—from coatings and plating, to shot peening, anodizing, and laser texturing—can significantly enhance a component’s wear resistance, corrosion protection, fatigue life, and even appearance.
What starts as a simple metal part can become high-performance through carefully tailored surface engineering. For example:
- Shot peening induces compressive stresses that inhibit crack initiation
- Anodizing creates a durable oxide layer that improves hardness and corrosion resistance
- Coatings like PVD and e-coat provide protective barriers against heat, chemical, or abrasive damage
- Laser texturing modifies friction or fluid behaviour in highly controlled ways
By adjusting parameters such as layer thickness, surface roughness, and process duration, engineers can fine-tune surface characteristics to meet demanding application requirements. This article delves into the mechanics behind each finishing technique, explains how they are applied in real-world scenarios, and helps engineers decide which surface treatment is best for the job.
Surface treatments are used to modify the surface of a material (metal, polymer, or wood) to make it more permeable to inks, paints, lacquers, adhesives, and other treatments, or more resistant to weather or chemical attack.
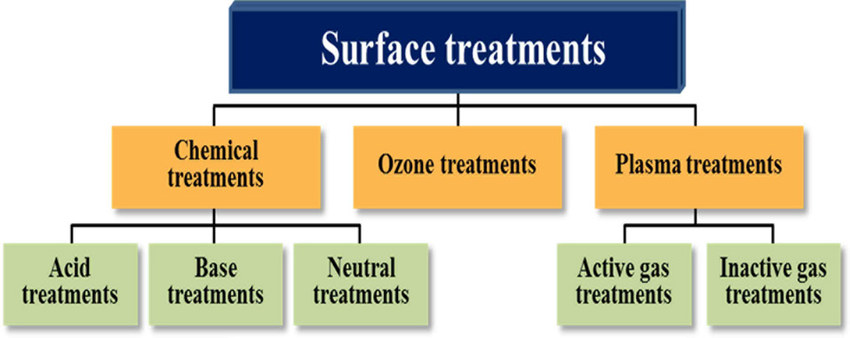
Cleaning, surface treatments, coating, and thin film deposition techniques are all part of surface processing operations. Cleaning refers to industrial cleaning procedures that get rid of impurities and dirt left over from earlier processing or the surroundings of the facility.
To remove dirt, grease, and other pollutants from a surface, cleaning techniques can be both chemical and mechanical. Surface treatments might be mechanical, like shot peening and sandblasting, or chemical, like diffusion and ion implantation. The outside surface of the work component is coated with material using coating and thin film deposition methods. Common coating techniques include porcelain enamelling, anodizing aluminium, organic coating (also known as painting), and electroplating. Physical vapour deposition and chemical vapour deposition are two methods used in thin film deposition to create exceedingly thin coatings of different materials.
The procedures used to add a layer of material to a surface include coating and thin film deposition. Metal products are virtually always electroplated, painted, or subjected to another procedure to add a coating (such as chrome plating).
The main purposes of coating a metal are to:
- prevent corrosion,
- improve product appearance (for example, by giving it a specific colour or texture),
- increase wear resistance and/or reduce friction on the surface,
- improve electrical conductivity,
- improve electrical resistance,
- Prepare a metal surface for further processing,
- Rebuild surfaces that have been worn down or eroded over time.
Industry-specific cleaning methods
Most workpieces require cleaning at least once over the course of production. This cleaning is accomplished through the use of mechanical or chemical techniques. When cleaning using chemicals, the workpiece’s surface is cleaned of undesirable oils and dirt. Mechanical cleaning is the process of removing materials from a surface using various mechanical actions. These processes frequently perform additional tasks like burr removal, smoothness improvement, sheen addition, and surface property enhancement.
Chemical cleaning processes
Various coatings, oils, dirt, and other pollutants typically cover a component’s surface after manufacturing. Even while some of these chemicals might have positive effects (like the oxide film on aluminium), it is usually preferable to clean the surface of impurities.
This section surveys the main chemical cleaning methods employed in industry while also discussing some general cleaning considerations.
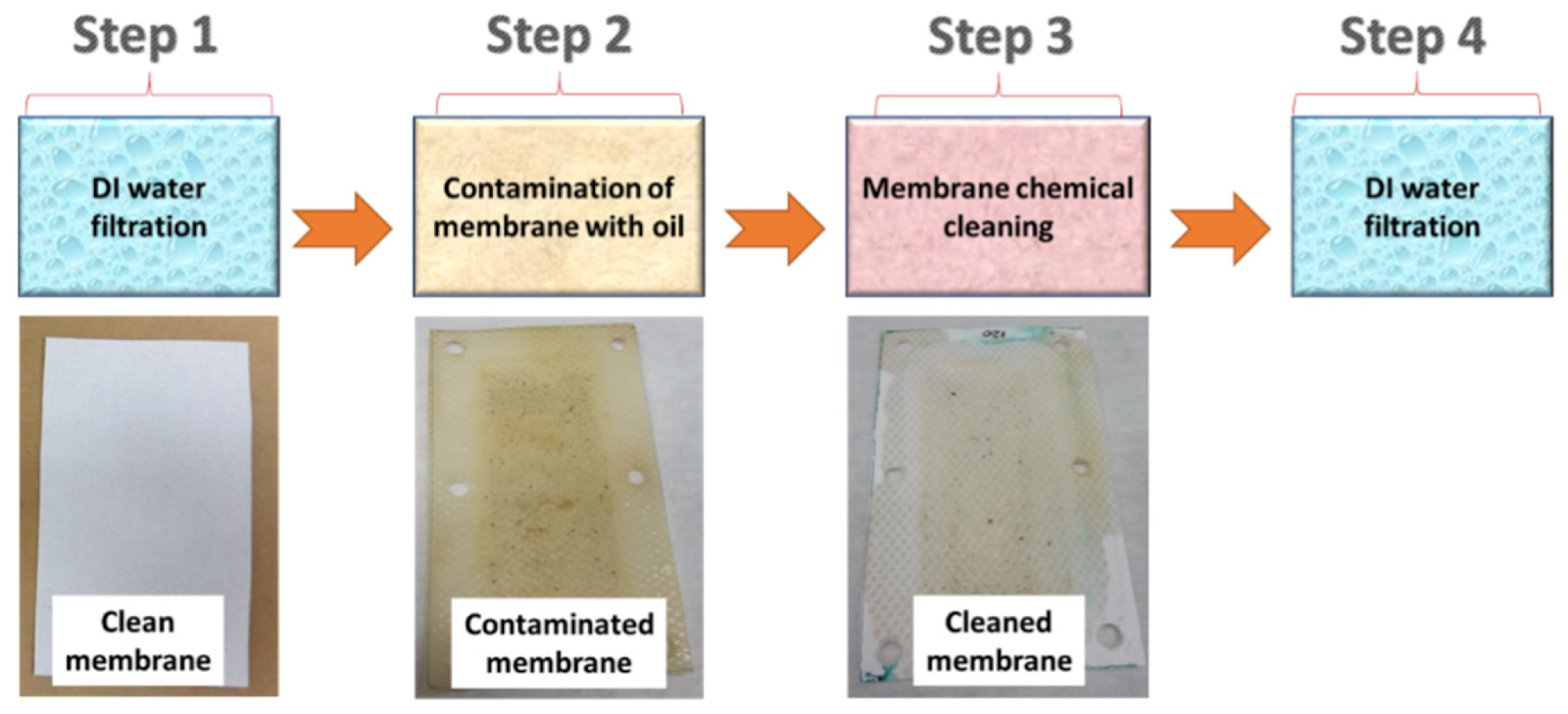
Cleaning manufactured parts (and products) is necessary for a number of reasons, including the following:
- to prepare the surface for subsequent industrial processing, such as coating application or adhesive bonding;
- to improve worker and customer hygiene;
- to remove contaminants that might chemically react with the surface;
- to improve the product’s appearance and functionality.
Choosing a cleaning method
There isn’t a single cleaning technique that can be applied to every cleaning job. Similar to how different soaps and detergents are needed for various domestic tasks (laundry, dishwashing, pot washing, bathtub cleaning, etc.), multiple cleaning techniques are necessary to address diverse cleaning issues in business. When choosing a cleaning technique, it’s important to consider the following factors:
- the contamination to be removed;
- the level of cleanliness required;
- the substrate material to be cleaned;
- the cleaning’s purpose;
- environmental and safety considerations;
- the size of part and geometry;
- cost and production requirements.
On part surfaces, various pollutants accumulate, either as a result of earlier processing or the atmosphere in the factory. Finding out what needs to be cleaned is the first step in choosing the appropriate cleaning technique.
Surface pollutants typically fall into one of the following categories when they are identified in a factory:
- Grease and oil, which includes lubricants used in metalworking;
- solids such metal chips, abrasive grits, shop dirt, dust, and similar substances;
- buffing and polishing compounds;
- oxide coatings, rust, and scale.
Chemical cleaning removes contaminants from a surface by using a variety of chemicals, such as:
Alkaline cleaning:
The most often used industrial cleaning technique is alkaline cleaning. As its name suggests, it uses an alkali to remove oils, grease, wax, and many forms of particles off a metallic surface, including metal chips, silica, carbon, and light scale. Alkaline cleaning agents are composed of inexpensive, water-soluble salts like sodium and potassium hydroxide (NaOH, KOH), sodium carbonate (Na2CO3), borax (Na2B4O7), phosphates, and sodium and potassium silicates, along with surfactants and dispersants, in water. Cleaning is typically done by immersion or spraying at temperatures between 50 and 95 degrees Fahrenheit (120 and 200 degrees Celsius). After applying the alkaline solution, the alkali residue is eliminated with a water rinse. Alkaline-cleansed metal surfaces are frequently electroplated or conversion-coated.
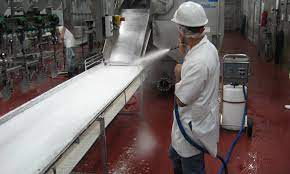
Electrolytic cleaning
Using a 3-V to 12-V direct current, an alkaline cleaning solution is subjected to electrolytic cleaning, also known as electro cleaning, in this related process. Gas bubbles are produced at the part surface as a result of the electrolytic action, which scrubs the surface and helps remove stubborn dirt films.
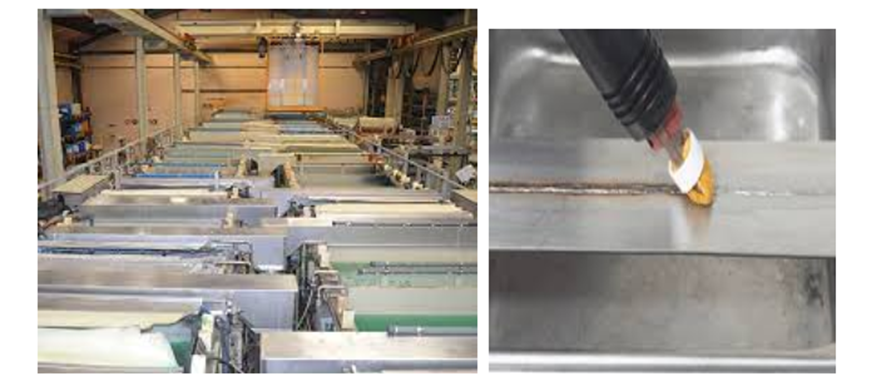
Emulsion cleaning
Organic solvents (oils) are distributed in an aqueous solution during emulsion cleaning. When adequate emulsifiers (soaps) are used, a two-phase cleaning fluid (oil-in-water) is produced that works by emulsifying or dissolving the dirt on the surface of the part. The procedure is applicable to both metallic and non-metallic parts. Before plating, all traces of the organic solvent must be removed using an emulsion cleaning procedure, followed by an alkaline cleaning procedure.
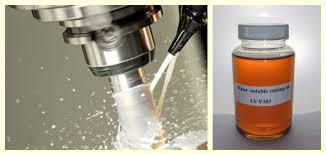
Acid pickling
Acid pickling is a more aggressive procedure to remove heavier oxides, rusts, and scales; it typically etches the metallic surface, which helps increase the adhesion of organic paint.
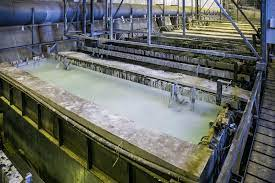
Mechanical cleaning processes
Through the use of abrasives or other comparable mechanical action, dirt, scales, or coatings are physically removed from the work surface of the work part during mechanical cleaning. In addition to cleaning, mechanical cleaning techniques are frequently employed for deburring and surface finish improvement. This method includes:
Shot Peening and Blast Finishing
Shot peening is the process of applying a high-velocity stream of tiny cast steel pellets (known as shot) to a metallic surface in order to cold work and introduce compressive stresses into the surface layers. The main purpose of shot peening is to increase the fatigue strength of metal components. The process of shot peening involves cold working to induce compressive residual stresses onto a component’s surface, leading to a change in its mechanical properties. By reducing the stress profile and enhancing strength, this technique is commonly used to improve the performance of various components. In spite of the fact that surface cleaning is a by-product of the process, its goal is different from blast finishing.
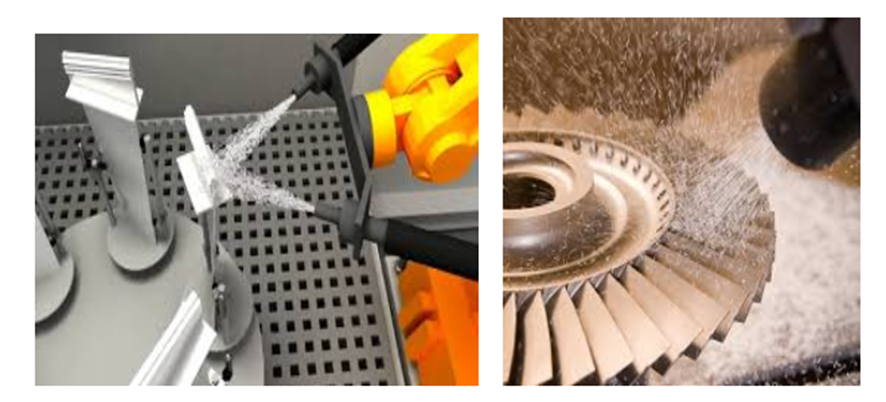
In blast finishing, a surface is cleaned and finished using the high-velocity impact of particle media. Sand blasting, the most popular of these techniques, employs sand grits (SiO2) as the blasting media. Other materials, such as soft materials like nylon beads and broken nut shells, as well as hard abrasives like silicon carbide (SiC) and aluminium oxide (Al2O3), are also used in blast finishing. Pressurised air or centrifugal force is used to drive the media toward the target surface. In other applications, the procedure is carried out wet, in which case small water slurries are aimed towards the surface by hydraulic pressure
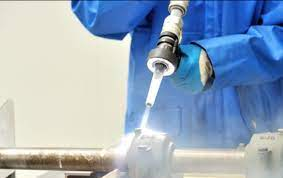
Tumbling and Other Large-Scale Finishing
Tumbling, vibratory finishing, and many centrifugal force-based procedures are examples of mass finishing. In tumbling, which is also known as barrel finishing and tumbling barrel finishing, pieces are combined by rotating the barrel at speeds ranging from 10 to 50 rev/min. The barrel is horizontally oriented and has a hexagonal or octagonal cross-section. A “landslide” action of the media and pieces as the barrel turns accomplishes finishing.
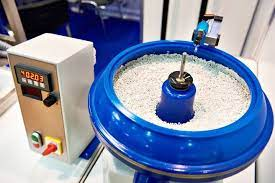
Mass finishing is the process of finishing pieces in bulk while combining them in a container, frequently with abrasive media present. To produce the desired finishing action, the mixing forces the components to rub against the media and one another. Deburring, descaling, deflashing, polishing, radiusing, burnishing, and cleaning are all mass finishing techniques. The components include extrusions, forgings, castings, stampings, and machined pieces. To achieve the appropriate finishing results, these mass finishing processes are occasionally applied to objects made of plastic and ceramic.
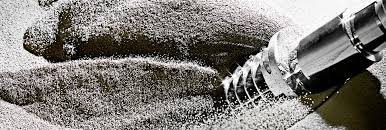
Ion implantation and diffusion
In this instance, the chemistry and characteristics of a substrate are changed by the surface being impregnated with foreign atoms. The process may include the following:
Diffusion : Diffusion is utilised in metallurgical applications to change the surface chemistry of metals in a variety of procedures and treatments. Surface hardening, which is characterised by carburizing, nitriding, carbonitriding, chromizing, and boronizing, is one such example. One or more elements (C and/or Ni, Cr, or Bo) diffuse through the surface of iron or steel during these treatments.
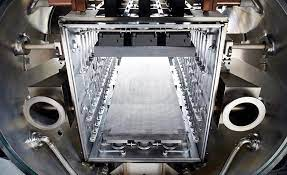
Ion implantation :When diffusion is impractical due to the high temperatures needed, ion implantation is a viable option. A high-energy stream of ionised particles is used in the ion implantation technique to embed atoms of one (or more) foreign elements into a substrate surface. The physical and chemical characteristics of the layers close to the substrate surface change as a result.
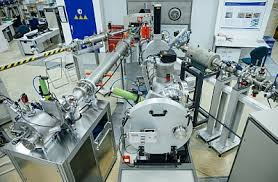
Plating and similar processes
Plating involves the coating of a thin metallic layer onto the surface of a substrate material. The substrate is usually metallic, although methods are available to plate plastic and ceramic parts. The most familiar and widely used plating technology is electroplating.
Electroplating :The electrolytic process of electroplating, also known as electrochemical plating, involves the deposition of metal ions from an electrolyte solution onto a cathode workpiece. The source of the plate metal is the anode, which is typically constructed of the metal being plated. A direct current is sent between the anode and the cathode from an external power source. The movement of plate metal ions in solution allows the electrolyte, which is an aqueous solution of acids, bases, or salts, to conduct electric current. Parts must be chemically cleaned right before electroplating in order to achieve the best results.
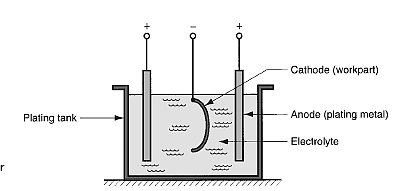
Electroforming: Although this procedure is almost identical to electroplating, it serves a very distinct purpose. Metal is electrolytically deposited onto a pattern during electroforming until the desired thickness is reached; the pattern is then removed, leaving the formed item. Electroformed items are frequently significantly thicker than ordinary plating, which has a 0.05 mm (0.002 in) or less thickness, hence the production cycle is proportionally longer.
Electroforming patterns can be permanent or disposable. Solid patterns have a shape or taper that makes it possible to take the electroplated section off. Expendable patterns are employed when the geometry of the part prevents the use of a solid pattern; they are eliminated during part removal. Fusible or soluble materials make up expendable patterns.
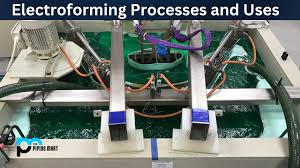
Application of surface treatment finishes
Surface finishes have numerous uses in a range of fields and contexts, including:
1. Automotive: In the automotive industry, surface finishes are utilised to increase the performance and sturdiness of items like engine parts, gears, and bearings.
2. Aerospace: Surface treatments are utilised in the aerospace sector to enhance the functionality and toughness of elements like structural members, landing gear, and engines.
3. Medical: In the medical field, surface finishes are utilised to enhance the functionality and robustness of parts including surgical instruments, implants, and prosthetics.
4. Industrial: In the industrial sector, surface finishes are utilised to increase the performance and sturdiness of parts including valves, pumps, and gearboxes.
5.Consumer items: In the consumer products sector, surface finishes are used to enhance the aesthetic and functionality of goods including electronics, appliances, and sporting goods.
6. Military: In the military, surface finishes are employed to increase the functionality and sturdiness of parts including weapons, vehicles, and protective gear.
7. Oil and gas: Surface coatings are employed in the oil and gas sector to enhance the functionality and robustness of parts including pipes, valves, and fittings.
8. Construction: In the construction sector, surface finishes are used to enhance the aesthetic and functionality of building materials including wood, concrete, and steel.
Interested in our engineering courses?
We have over 70 courses across all major engineering disciplines, including, mechanical, electrical and electronic, civil, aerospace, industrial, computer and general engineering. Visit our course catalogue for a complete list of fully accredited engineering programmes.
A small selection of short courses …
Level 6 Courses
International Graduate Diploma in Mechanical Engineering
Level 5 Courses
Higher International Diploma in Industrial Engineering
Higher International Diploma in Mechanical Engineering
Level 4 Courses
Higher International Certificate in Industrial Engineering
Higher International Certificate in Mechanical Engineering
Alternatively, you can view all our online engineering courses here.
Recent Posts
From Sparks to Strength: Top Welding Techniques You Should Know
From Sparks to Strength: Top Welding Techniques You Should Know Introduction From spark to structural bond—that’s the transformative power of welding. In the iLearn Engineering® article “From Sparks to Strength: Top Welding Techniques You Should Know,” readers are guided through essential welding methods—such as SMAW, MIG, TIG, and spot welding—each selected for strength, speed, or […]
How Material Removal Rate Affects Surface Quality and Production Speed
How Material Removal Rate Affects Surface Quality and Production Speed Introduction When machining components, one of the most critical—and often overlooked—factors is the material removal rate (MRR). It’s a common assumption that increasing MRR boosts productivity. However, as this iLearn Engineering article explains, this simple equation comes with important trade‑offs. Pushing MRR too high can […]
How Manufacturing Affects the Mechanical Properties of Materials
How Manufacturing Affects the Mechanical Properties of Materials Introduction Manufacturing doesn’t just shape a material—it fundamentally alters how it behaves. Engineers often select materials based on desired properties like strength, ductility, hardness, or fatigue resistance. But those properties are not fixed. They evolve throughout the manufacturing process. This article explores how processes such as casting, […]